Solutions for manufacturing
In manufacturing there are so many challenges and risks – from pricing of raw materials, long lead times, heavy investment in equipment, managing maintenance and downtime, and optimising output despite capacity constraints.
How can you connect your data, gain greater visibility and streamline operations?
Solutions for manufacturing
By their nature, manufacturing organisations are complex and operate in a volatile, ever-changing market with competitive threats from developing economies. Managing budgets and plans in this environment is equally complex.
Imagine having sales and operational budgets tightly integrated with production and capacity plans, whilst maintaining visibility over forecast profitability of product lines and cost allocations.
With the right technology, you can create and update multiple driver-based models and see the impact of these changes on profit, cashflow and inventory holdings. You can also easily manage rolling forecasts and model out numerous scenarios quickly and effectively.
Protect your business from external threats and help it reach its potential.
Watch an example of how you can conduct scenario planning for manufacturing.
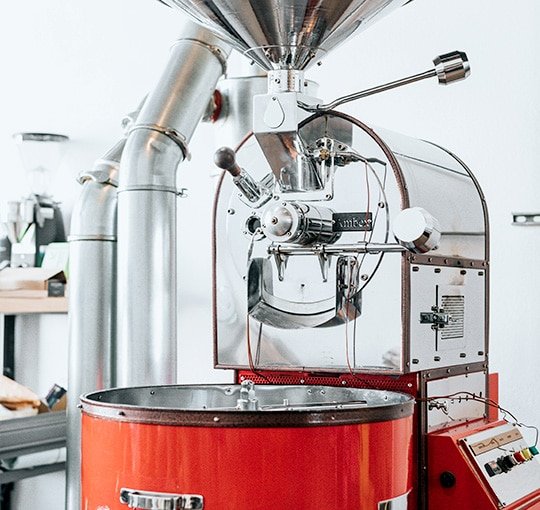
Manufacturing organisations typically leverage multiple systems to perform vital functions such as new product development, setting up and managing bills of materials, or leveraging sales forecasts to drive manufacturing plans.
To support these activities, consistency of master data in relation to entities such as raw materials, finished products, suppliers, and plant and equipment is vital, but increasingly difficult and time consuming to manage.
Using the right solution, manufacturers can easily connect siloed technology platforms and manage master data across the organisation, ensuring the originating system of record is correctly updated and synchronised across all systems.
This drives efficiency, accuracy and a single source of truth for operational processes and analytical reporting.
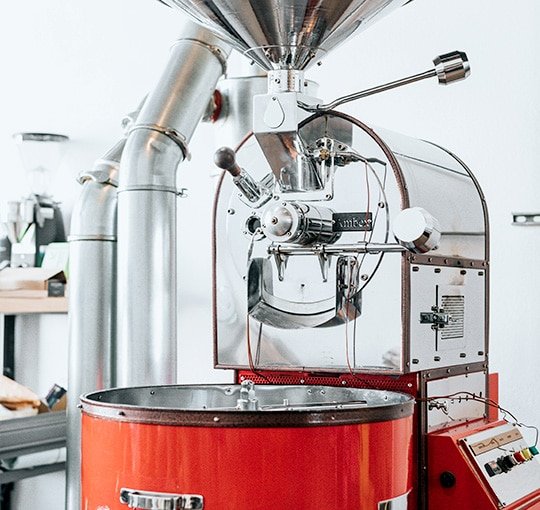
Simpler, more transparent and intelligent
Ballantyne traditionally relied on spreadsheets and legacy reporting tools for budgeting, forecasting and reporting. Learn how their fit-for-purpose tool enabled them to:
∙ Assess the bottom-line impact of pricing decisions
∙ Close the loop between transactional and reporting systems
∙ Adopt a rolling forecast to ensure alignment with market
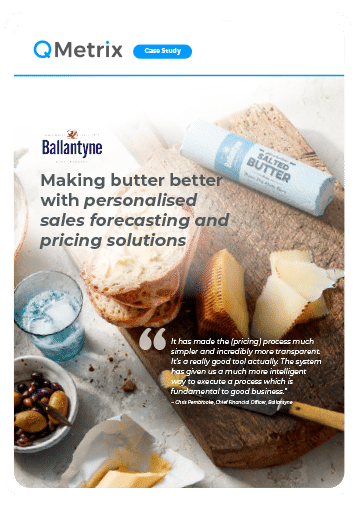
At QMetrix our solutions empower you to operate with the agility needed in today’s business environment. We work together to deliver the right outcome for your unique manufacturing business.
Some of our manufacturing clients








